This year, we participated in the NREL Wind Drivetrain Reliability Collaborative Workshop from February 17 to 19, 2025, in Golden, Colorado, which corresponds with Engineer’s Week.
Harnessing AI and Digital Engineering for Wind Reliability
The first day focused on machine learning and AI research and development; day two focused on main bearings and greasing; and day three focused on condition-based maintenance of the system from generator to blades.
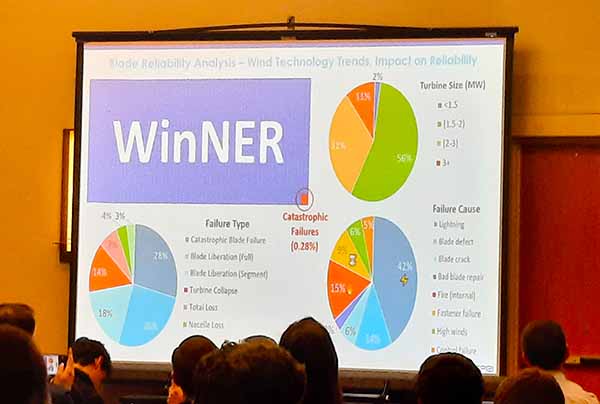
Figure 1: Discussion of NREL reliability database.
The Engineering Week reference is incidental to the meeting. However, it represents a national celebration in the USA dedicated to recognizing the contributions of engineers and inspiring the next generation of innovators.
It is organized annually by the National Society of Professional Engineers (NSPE) in collaboration with various engineering organizations, schools, and companies. Engineers Week was founded in 1951 and is meant to promote STEM education and engineers’ vital role in shaping society.
It includes educational outreach programs for students, public awareness campaigns, networking events and recognition for engineers, and competitions and hands-on activities to engage future engineers.
The result was that the NREL event was perfectly, but unintentionally, set.
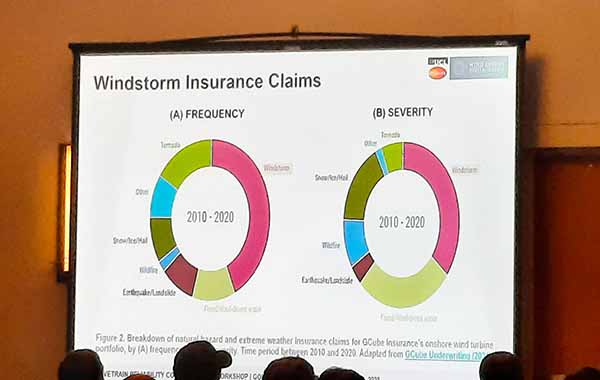
Figure 2: Weather-related reliability.
The first day, February 17, was a half-day event in the afternoon, separated into presentations and discussions on digital engineering, digital reliability, and maintenance research and development. A majority of the work was related to modeling methods and AI approaches, which showed similar progress to the prior year.
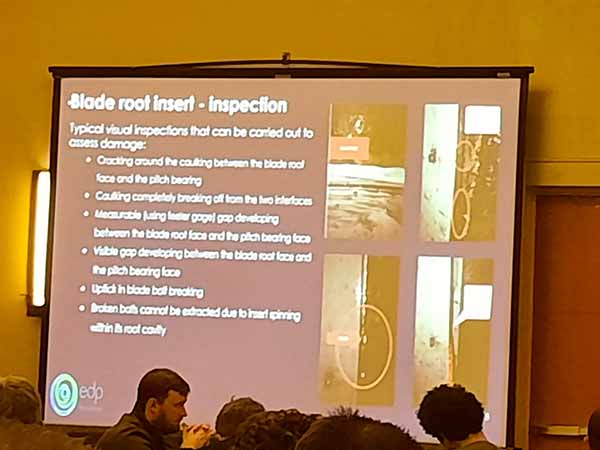
Figure 3: Blade failure condition-based maintenance and failure modes discussion.
To put this into perspective, funded projects related to what we discuss in the industry, such as modeling blade and gearbox performance, including digital twins, are needed. Presentations were from the Electric Power Research Institute (EPRI), Aarhus University, WEC Energy, and Amazon (AWS) for Digital Engineering.
The results were enlightening as these were research projects and not sales presentations.
The presentations were good, except that they did not involve real data, something that provides a barrier to applications. However, the exercises identify the opportunities associated with the potential to apply digitalization and the potential difficulties. The results were enlightening as these were research projects and not sales/marketing presentations.
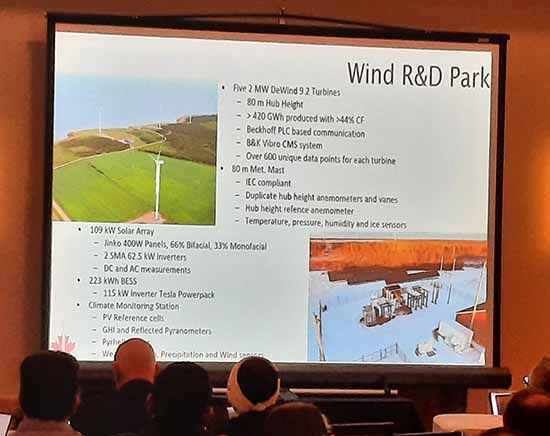
Figure 4: WEICAN research wind and solar park.
The digital O&M R&D sessions involved universities primarily using model-generated data for physics and AI-driven approaches for offshore wind, gearbox vulnerabilities assessment, and turbine performance and prognostics.
The presentations were also very good and represented the most advanced work in this area. They also identified the present limitations and what we must do to advance technologies. It also echoed another consideration: that simple solutions can be complicated by applying ML and AI.
Advancements in Bearings, Lubrication, and Powertrain Performance
On February 18, we discussed gearbox and main bearing measurement technologies from NREL’s work on fiber optic sensors, wind turbulence impact on main bearing reliability, and work on hydrodynamic journal main bearings.
Most present main bearing technology for land-based wind turbines involve double-roller and spherical bearings. The projects involved a discussion of solutions for the mechanical impacts on the powertrain, including finite element analysis work.
This led to the following discussion on lubrication as an asset with presentations on measuring energy efficiency improvements from lubrication, gear oil asset management, and impacts of steel quality inspections and finding inclusions in bearings.
The presenters and researchers were primarily lubrication and bearing manufacturers such as Castrol, ExxonMobil, and NSK. Much of the data will carry over to industrial applications which we may explore in a future article.
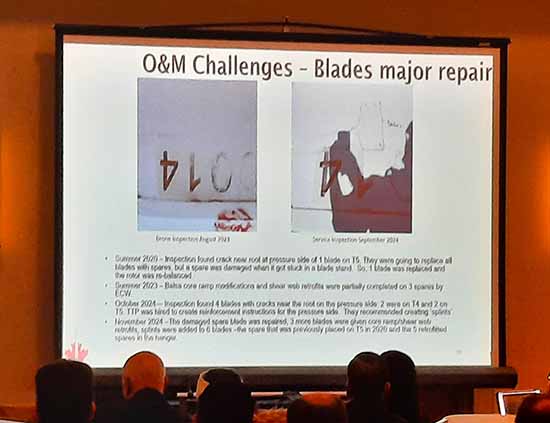
Figure 5: An example of where a drone and AI missed a fractured blade caught during a technician inspection.
One of the sessions I attended related to our work with multiple OEMs and wind site owners on main bearing reliability. One of the discussions resulted in developing a working group led by MotorDoc that involved additional testing methods (i.e., the EMPOWER) for high-frequency analysis and floating nacelle currents.
The study group includes multiple wind site owners, OEMs, brush manufacturers, bearing manufacturers, lubrication manufacturers, NREL, and several other researchers. Results will be presented at the next powertrain meeting at Argonne National Labs in 2026.
They will focus on the main bearing, gearbox, generator bearing fluting, electrical discharge damage, and prospective solutions. This problem is over a decade old. The group determined it was time to move beyond modeling and basic mapping, which was performed with the EMPATH ESA system, and utilize a combination of field measurements, investigations, and data science—finally subjecting the issue to a full RCFA.
Condition Monitoring: Innovations in Predictive Maintenance
On February 19, following a very active set of Tuesday sessions, we moved to condition monitoring considerations, starting with discussions of technologies that require investigation. The earlier part of the day focused on acoustic, oil, vibration, and several other technologies and ended with the studies performed with EMPATH, EMPOWER ESA, and MCSA.
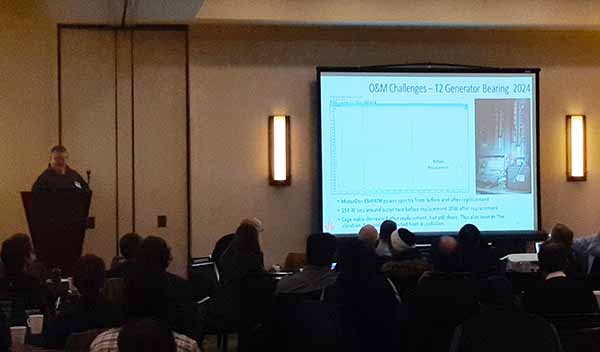
Figure 6: Discussion of ESA before and after detection of bearing defects.
Presentations included Poseidon’s work on oil debris-enabled life extension, including how sensing is performed; Onyx Insight and EDP Renewables’s challenges of blade root connection failure and proactive maintenance; and SkySpecs’ AI-powered evolution of drivetrain diagnostics.
The first two were practical field studies, and the last presentation was primarily a primer on common machine-learning techniques.
The final group of presentations started with a presentation by WEICAN (Wind Energy Institute of Canada) covering the site’s history in PEI, challenges they’ve run into, technologies they have deployed, and comparing EMPATH and EMPOWER technologies to their vibration equipment.
This final work is related to the early detection of a generator bearing before and after replacement, with the visual inspection to be performed within the next month by Mobil.
CC Jensen gave the following presentation on the impact of oil cleanliness and condition monitoring, in which filter sizes were discussed up to optimization for maximum equipment life.
The program ended with a panel discussion about O&M field experience with RWE, Orsted, EDF, and Engie, all wind owners. This also identified the primary CBM technologies of vibration, ultrasonics, and electrical signature analysis.
The information and ability to network with more than 250 engineers representing owners, researchers, testing technologies, OEMs, lubrication manufacturers, and other stakeholders provided pathways to determine and implement additional studies.
Collaboration and Future Research in Wind Energy Reliability
One of the great things about NREL is the ability to provide a voice and inroads for small to large businesses, developers, OEMs, and other stakeholders to work together with resources that would otherwise be unavailable to small businesses.
In our primary focus, MotorDoc partnered with WEICAN through NREL contacts to identify and compare ESA and MCSA, using EMPATH and EMPOWER, to vibration analysis of generator bearings, with additional studies planned for the remainder of the system.
This helps expand the options for site owners and OEMs for machine prognostics. The project involved the supply and support/training of Framatome and MotorDoc technologies as our contribution to the project
The coordinated research project has resulted in some independent results, allowing us to improve our systems to provide even greater results. We have truly enjoyed our collaboration with WEICAN and the relationships that have resulted in fantastic results for the USA, Canada, and other international stakeholders.
In addition, wind, solar, hydrogen, energy storage, and other technologies have provided systems to NREL to provide a proving ground for new technology and research that directly impact small and disadvantaged businesses with low risk for alternative energy site owners.