In a critical section of the paper machine, early signs of bearing failure in a guide roll were identified without online monitoring, relying solely on targeted condition-based measurements.
This case study outlines how a rapid increase in acceleration levels triggered a focused diagnostic effort, despite the roll’s difficult location behind the frame and the added complexity of requiring wire replacement if the roll was changed.
Through persistent monitoring and strategic decision-making, the team avoided unplanned downtime, executing a planned intervention that preserved system integrity and prevented a major functional failure.
What the Data Revealed: From Subtle Signals to Clear Alarms
Monitoring began in January 2025 when the equipment condition shifted from normal to alert, indicating bearing wear. Due to the difficult access location, any intervention was more complex since the roll is positioned behind the chair. In February, the condition escalated from alert to alarm, reinforcing the recommendation for bearing replacement.
As an immediate action, we increased the flow rate of the rotameters and continued to monitor the asset more frequently until the intervention could be scheduled.
Given the complexity of accessing the location, which required cutting the screen, and considering the elevated vibration values indicating a high risk of functional failure, the decision was made to replace the entire roll.
Corrective Actions and Implementation Plan
An RDP (Predictive Diagnosis Report) was issued indicating the bearing housing, and the roll replacement was requested.
After the roll replacement, an improvement in the vibration levels was observed.
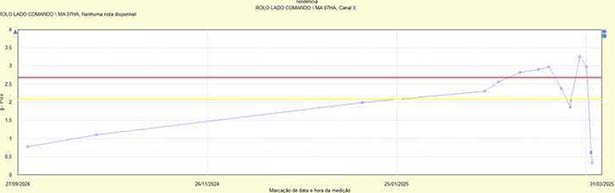
LC (Acc)
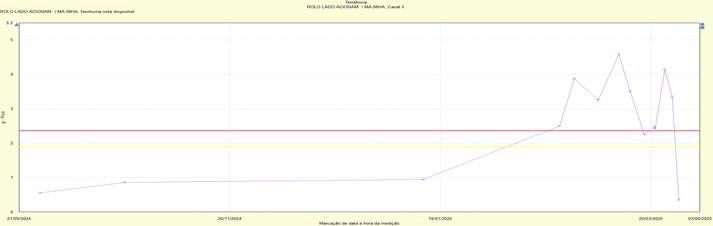
LA (Acc)
Critical Failure Prevention
Early defect identification was crucial in preventing more severe damage to the equipment, such as failure of the bearings, housings, shafts, or even the roll itself.
Operational Safety and Availability
The intervention addressed the immediate issue and ensured continued operation, preventing unexpected downtime and safeguarding the equipment assembly. Vibration analysis proved to be an essential tool for optimizing predictive maintenance and the operation of rotating machinery.
Scheduled Intervention
Performing maintenance interventions during scheduled shutdowns is a key strategy in industrial maintenance, allowing for correcting potential failures without compromising operational performance or causing unplanned downtimes.
A functional failure of the assembly could have resulted in a complete machine stoppage.
Key Outcomes and Lessons Learned
Vibration analysis proved to be an essential tool for the early detection of failures and for supporting strategic decision-making in the maintenance of critical equipment. The swift and efficient intervention prevented a catastrophic system failure and generated significant cost savings, ensuring operational continuity and maintaining a safe production environment.