“My maintenance staff is highly trained and do not like using procedures.”
If the statement above is valid, and the cost of asset failure is not important to our operation, then your staff must have an unlimited and infallible memory – congratulations!
Did you know that the most complex piece of equipment ever built was a nuclear submarine, and that the first nuclear submarines experienced catastrophic failure due to a lack of effective procedures?
If safety is number one in your organization, repeatable, effective work procedures should also be.
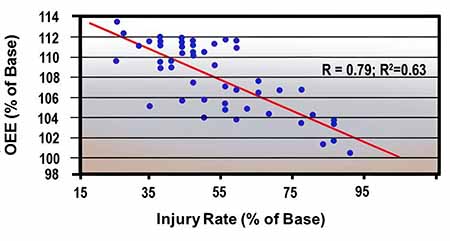
Figure 1: Injury Rates
The Safety Manager cannot make the facility safe:
- Support facility with tools, training, facilitation, measures, etc.
- Safety is everyone’s responsibility.
The Reliability Manager cannot make the facility reliable:
- Support facility with tools, training, facilitation, measures, etc.
- Reliability is everyone’s responsibility.
(Figure 1 and the above data are from Making Common Sense Common Practice: Models for Manufacturing Excellence by Ron Moore.)
To ensure that you have a safe work environment, you must have a reliable one and repeatable, effective procedures are a requirement. Without a repeatable procedure, you have chaos.
Awareness Is the First Step Toward Change
“We have learned to live in a world of mistakes and defective products as if they were necessary to life.” – Dr. W. Edward Deming
There are a few things to look for with your maintenance staff. Remember, errors or areas of concern are not their fault at this time; however, it is time to change.
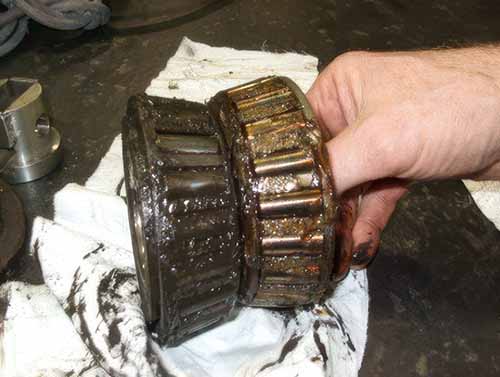
Figure 2: Bearing Failure
We may not know why this bearing failed, but looking at Figure 2, it is easy to surmise that the correct lubricant, quantity, and re-lubrication interval were likely not clearly specified in the equipment’s maintenance instructions.
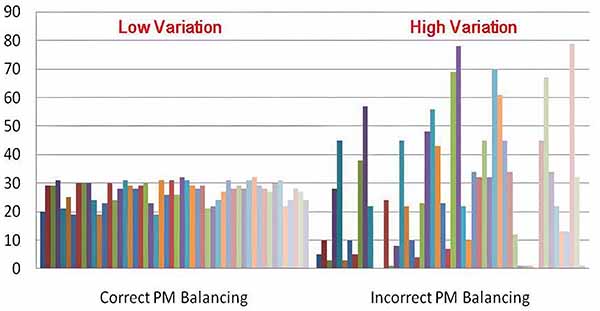
Figure 3: Balancing Your PM Execution for the Year (Sample)
- Are torque wrenches being used by mechanics and electricians? If they are not, you are having component-level failures that you should not be experiencing.
- Are specifications for bearing lubrication known and being followed?
- Does anyone know the hydraulic fluid micron level required for critical hydraulic systems?
- Are PMs executed with PM variation? For example, a 30-day PM may be accomplished on the 3rd of the month this month and on the 20th of the month next month, resulting in equipment problems. PM is a “controlled experience” and, as such, requires repeatable, effective, and on-time procedures. (See Figure 3.)
- Is PM being performed on equipment that continues to experience total and partial functional failures?
- Is the use of a torque wrench for hydraulic fittings seen as not important, yet leaking fittings are always a problem? Remember, oil out means contamination in.
- Are maintenance staff and contractors welding on equipment without using known Best Practices?
- Does everyone truly understand their roles and responsibilities when it comes to procedure development and execution?
To help make roles and responsibilities clear during the procedure development process, use a RACI Chart like the one shown in Figure 4 to identify the specific tasks and individual responsibilities.
R – Responsible: The Doer
A – Accountable: The “buck stops here” (only one person can be accountable)
C – Consulted: Two-way communication
I – Informed: One-way communication
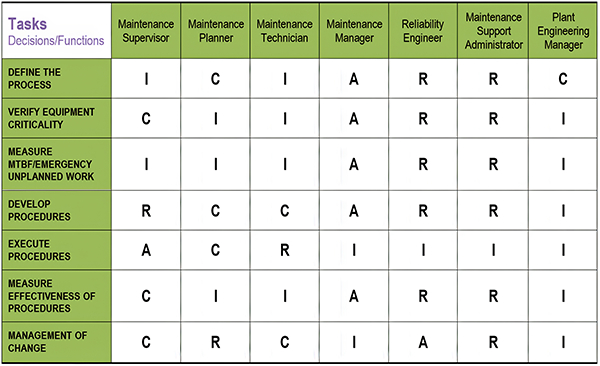
Figure 4: Sample RACI Chart for Work Procedures
Procedure-Based Maintenance – Can You Live Without It?
Yes, of course one could live without procedure based maintenance; however, there can be consequences with any decision one makes.
The final expected result from any procedure based maintenance organization is that the human factors for variation (human error) in the maintenance process are mitigated or eliminated. This results in higher asset availability and reliability. Unfortunately, few companies can achieve this status.
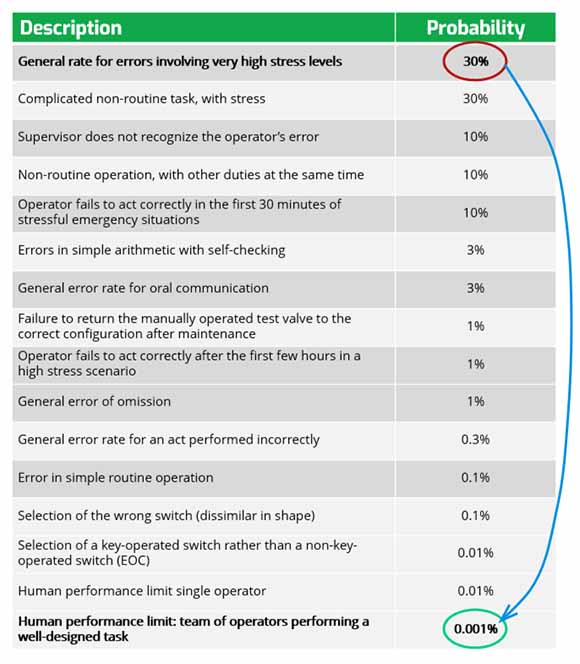
Figure 5: Human Error Rate
In the field of maintenance, the traditional approach has been to rely on the intuitive knowledge and skill of the craftspeople who conduct it. There is a great deal of pride of workmanship and, in too many organizations, a great deal of psychic income in addition to significant overtime pay for successful emergency repairs to return equipment to operation after unplanned shutdowns.
There is a mystique that accompanies all of this that many skilled craftspeople would like management to believe firmly: there are too many variables in maintenance, which makes compliance with written procedures impossible and impractical, and the “way we have always done it” is the best and only way to conduct maintenance.
This idea spills over into preventive maintenance, as well. Examples:
- Check the pump
- Check the seals for leaks
- Check bearings for noise
- Lubricate the bearing until grease comes out
A typical craftsperson believes that intuitive knowledge is preferable to a written procedure and a thoroughly defined checklist. Aside from these problems, most organizations have allocated no resources to the creation and ongoing support of procedures and checklists.
Accordingly, these organizations are focusing on the wrong way of conducting maintenance to obtain optimized asset reliability at an optimal cost.
What Are They Thinking?
“Maybe a craftsperson has an unlimited or infallible memory…”
Is it possible? Yes, for a robot or computer. Is it probable? No.
Think about how many times a maintenance person
must return to the maintenance shop because he did not have the right tool, part, information, etc.
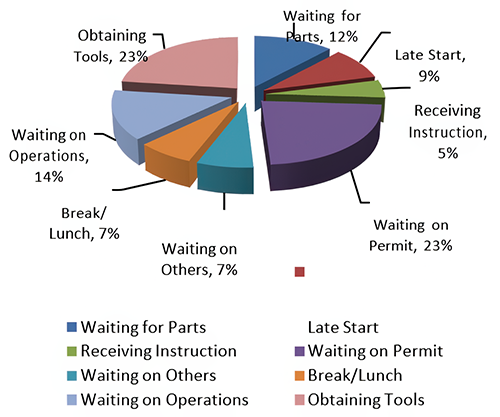
Figure 6: Sample Wrench Time Losses
This method of thinking and experimenting results in at least a lost opportunity for increased profits from existing assets. If a company is not aware of this loss, then is it truly a loss?
Management is gambling with profits and losing big time with the approach that emphasizes pride of workmanship over an approach that has been proven to work.
Ensuring and Sustaining Reliability
Lost in all of this is the concept of ensuring and sustaining reliability as both corrective and preventive maintenance are performed.
Ideas about how things fail that we used to rely on as a basis for preventive maintenance have been shown in failure profile studies over the past 40 years to apply to only a minor percentage of failures. In gambling terms, this means that odds are very long against a “win”. From this it can be shown that time
directed maintenance, in general, should also apply to only a minor portion of the failure modes that an organization must correct or mitigate. (See Figure 7.)
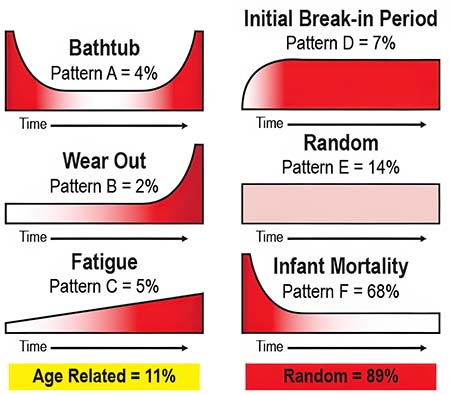
Figure 7
Furthermore, it can be shown that intrusive, time-directed maintenance can be detrimental to reliability because humans are involved and they produce “infant failures”.
Instead, nonintrusive maintenance and monitoring tasks should be sought. Indeed, because of the known distribution of failure profiles, the only logical approach for mitigating failures in the majority of equipment is through the use of nonintrusive tasks supported by procedures to ensure consistent results.