The effort to save energy is seldom viewed beyond the components when, in fact, energy efficiency requires an understanding of the systems involved.
Over the past almost four decades in the industry, with about 35 years involved in energy and energy efficiency, I’ve frequently observed companies increase their energy consumption by taking a component approach. This is often the case in variable torque fan, pump, and compressor applications where affinity laws come into play.
True energy efficiency demands a shift from component fixes to system-wide understanding.
When we consider the affinity laws, one of the more important ones in fans, pumps, and related loads is that the horsepower requirement increases with the cube of the speed. Of course, this is an approximation and proper selection of the driven equipment to its curve, and BEP (Best Efficiency Point) is crucial for optimal energy use.
When applied to VFDs, you will also note that the BEP curve changes but will have a maximum and minimum speed and related horsepower requirement.
Information related to this can also be found on the US Department of Energy’s programs (note that the address can change): Motor Systems | Department of Energy, which includes links to all of the other resources we developed in the Challenge programs in the 1990s and updated around 2010.
One of the opportunities for belt and sheave systems is an improvement in coupling efficiency by moving from a regular belt to a cogged belt, which allows for more surface area contact and less slip, or a synchronous belt, which is effectively a timing belt. While a cogged belt can move coupling efficiency from <90% to 90-95%, a synchronous belt is often between 95-98% efficient.
However, a lot of considerations must be taken into account, especially if included with a variable frequency drive. This article will discuss improperly applying a synchronous belt to a fan application and the related impact.
The Importance of System-Wide Energy Analysis
Having tested the fan system several years before when applied with normal belts and sheaves, the original operating context and data were known. The motor is the same as the original test, which allows for a direct comparison between the past and present.
The original system had a 10-inch ID sheave at the motor and a 13.75-inch ID sheave at the fan side. At the point of operation tested with the original belts the motor load was 45.5% loaded with 31.4 Amps at 55 Hz, or 1638.4 RPM, and a fan speed of 1196.1 RPM. The electrical data can be found in Figure 1.
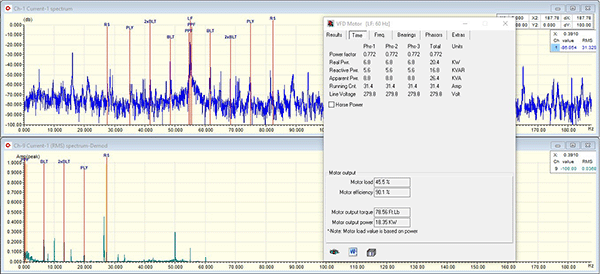
Figure 1. Original Fan Application
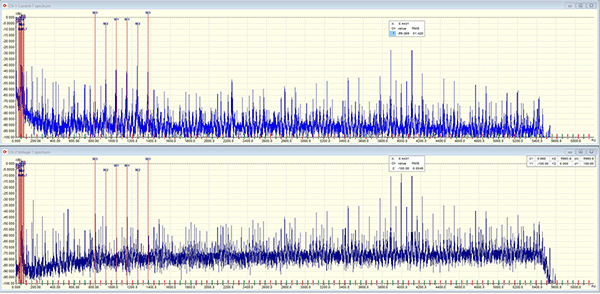
Figure 2: Original application including static eccentricity from too high belt tension.
The signatures in Figures 1 and 2 indicate over-tensioned belts and misalignment. At this time, no issues were detected with standard motor bearings.
Switching to a higher-efficiency component doesn’t guarantee lower energy costs—system-wide evaluation is key.
The frequency indicates some turbulence and the driven equipment rapidly changes speed across +/- 3 Hz as the load attempts to maintain a constant static pressure. The VFD is set up for about 90-second acceleration and deceleration linearly and has some over and undershoot. The high-frequency data set also shows the carrier frequency of the drive set to 4 kHz.
Evaluating the Impact of Synchronous Belts in Variable Torque Systems
The system was modified between the data above and the present, as shown in Figure 3. An addition of a synchronous belt of 123.46 inches, a motor sheave of 11 inches, and a drive of 12 inches diameter was installed—no changes to any other part of the system, including the VFD.
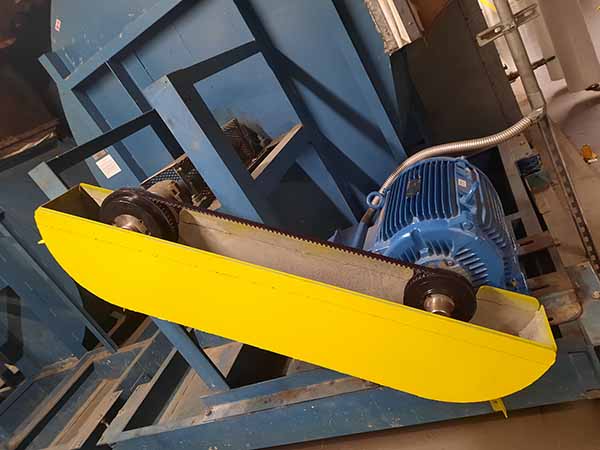
Figure 3: Motor Application with Synchronous Belt System.
The result is a driven speed of 1302.6 RPM, which is over 100 RPM of the original sheave design, at a motor speed of 1439.56 RPM and a drive output frequency of 47.99 Hz. Even with the decreased motor speed, the increased driven speed results in an RMS current of 86.24 Amps (average) with a resulting load of ~120%.
With an existing misalignment, significant belt noise, bearing issues, and winding stress from the VFD, the total energy consumption increased from the original 178,704 kWh/year to 474,802 kWh/year. This means, assuming $0.10/kWh and 0.699 metric tonnes of CO2/MWh, an increased use of 296,098 kWh/year, $29,610/year, and 207 metric Tons of CO2/year.
The VFD was also throwing an overload alarm in which the settings had been disabled to avoid ‘nuisance tripping.’ It should be noted that there is no such thing as nuisance tripping, just problems that have not been identified.
While the company is going back to determine what engineering changes are required or a switch to cogged belts, a VFD adjustment was made to reduce the shearing off of belt teeth and other damages, including driven equipment bearings.
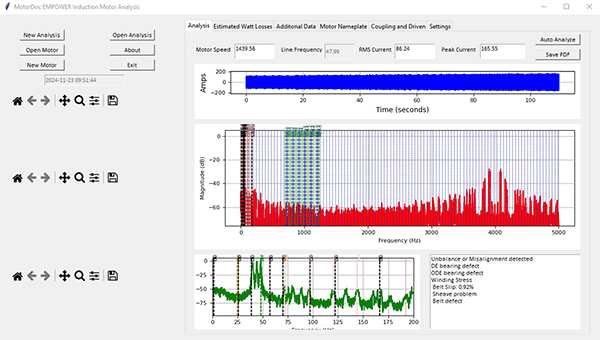
Figure 4: EMPOWER data basic findings related to conditions before VFD changes.
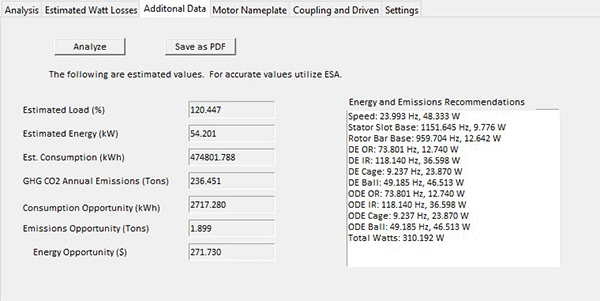
Figure 5: Energy Analysis of data, including component losses.
The conditions of components would only have an improvement of about 2717 kWh/year, 1.9 metric Tonnes of CO2/year, and $272/year, as shown in Figure 5.
Next, it is noted that the high-order harmonics (reference Harmonic Overload: Impacts Of High-Frequency Switching on Modern Electrical Systems) continue well out to the range of the spectrum (Figure 6), and it can be assumed beyond. This generates additional stator and winding heating and harmonics, reducing the motor efficiency by at least 2%.

Figure 6: High-order harmonics of 4 kHz VFD carrier frequency out to 22 kHz.
Optimizing VFD Settings for Energy Efficiency and System Longevity
The VFD settings were modified to include a change from a linear speed change to an S-curve and a speed change from 90 seconds to 120 seconds, but not modified for the static pressure.
The output speed of the drive based on the feedback was kept the same, so overloading was allowed in order to avoid driven equipment and process changes, which are critical. The gain was also modified to reduce damage from rapid speed changes, including static load effects.
As noted in Figure 7, the result is still a higher running speed, increased RMS current to ~155%, audible overload noise, and increased operating and sheave temperatures.
As other changes were not made, winding stress is still present along with the other conditions, there is less overshoot, but still changes in frequency and running speed. Overall, less stress exists mechanically while electrical conditions increase, and the drive continues to show an overload warning. It did trip during the initial data collection.
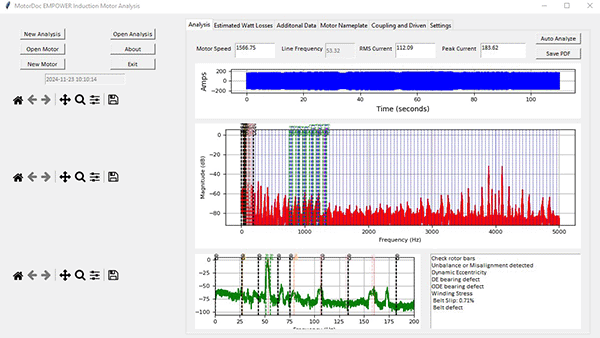
Figure 7: Findings after VFD corrections.
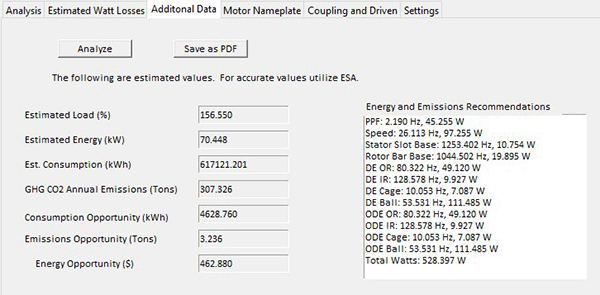
Figure 8: Component energy losses following VFD modifications.
The result is a much larger increase in overall operating energy usage and emissions, as shown in Figure 8. However, as shown in Figure 7 and Figure 9, the noise floor and peaks reduce, meaning that the effective electrical ‘force’ of the higher-order harmonics has reduced.
In this case, the overall increase in operating losses per year is an effective increase to an additional 438,417 kWh/year, which results in an increased operating cost of $43,842/year and 182 metric Tonnes of CO2/year.
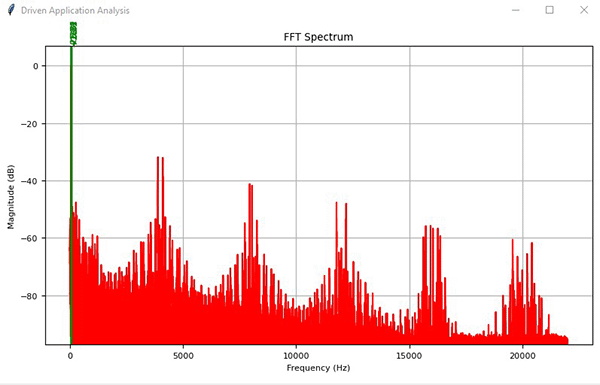
Figure 9: Reduced high-order harmonics of VFD carrier frequency following settings changed.
Lessons Learned: Avoiding Costly Energy Efficiency Mistakes
Energy efficiency measures without system consideration can result in costly mistakes and increased emissions.
A couple of approaches could have eliminated this error in installation:
- Keeping or replacing the original sheaves with sheaves of the same dimension and a change to cogged belts.
- The synchronous belt with sheaves the same dimension as the original.
- Modifications to the feedback loop related to the static pressure sensor and output speed to represent the changes in sheave sizes.
Switching to a higher efficiency component does not necessarily represent an improvement in energy and emissions, especially in variable torque applications.
A full and proper review of the application to measure the impacts of changes and methods to correct any defects in the application is required. This can be initially evaluated using modeling including through US DOE software such as MEASUR (MEASUR | Department of Energy).
Improper application of an energy-efficient measure without system consideration can result in extremely costly mistakes, operating costs, and CO2 emissions.
Howard W. Penrose, Ph.D., CMRP, CEM, CMVP, is president of MotorDoc® LLC, a Veteran-Owned Small Business. He chairs standards at American Clean Power (2022-25), previously led SMRP (2018), and has been active with IEEE since 1993. He represents the USA for CIGRE machine standards (2024-28) and serves on NEMA rail electrification standards (2024+). A former Senior Research Engineer at the University of Chicago, he’s a 5-time UAW-GM Quality Award winner. His work spans GM and John Deere hybrids, Navy machine repair, and high-temperature motors. He holds certifications in reliability, energy, M&V, and data science from Kennedy-Western, Stanford, Michigan, AWS, and IBM.