Most companies spend a lot of money training maintenance personnel to troubleshoot a hydraulic system. If we focused on preventing system failure, we could spend less time and money troubleshooting a hydraulic system.
We usually accept hydraulic system failure rather than deciding not to accept hydraulic failure as the norm. Let’s spend the time and money eliminating hydraulic failure rather than preparing for failure.
I worked for Kendall Company in the 1980s, and we changed our focus from reactive to proactive maintenance on our hydraulic systems, thus eliminating unscheduled hydraulic failures. We will discuss the right way to perform maintenance on a hydraulic system using the “Maintenance Best Practices.”
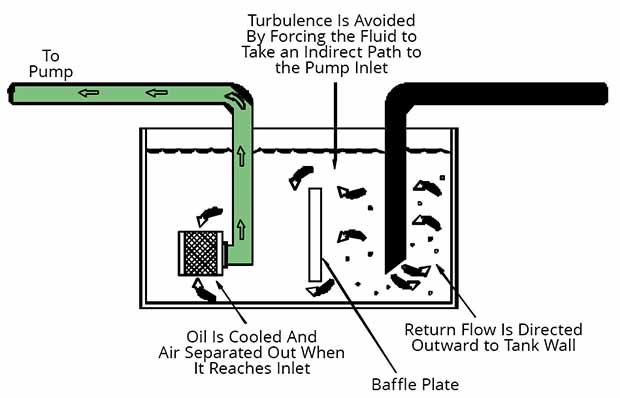
Hydraulic System
Key Pillars of Effective Hydraulic System Maintenance
Lack of maintenance of hydraulic systems is the leading cause of component and system failure, yet most maintenance personnel don’t understand the proper maintenance techniques for hydraulic systems. The basic foundation for performing proper maintenance on a hydraulic system has two areas of concern.
The first area is preventive maintenance, which is critical to the success of any maintenance program, whether in hydraulics or any equipment that we need to be reliable. The second area is corrective maintenance, which can cause additional hydraulic component failure when not performed to standard.
A lack of repeatable procedures with specifications will ensure many human-induced failures.
Preventive maintenance of a hydraulic system is fundamental and straightforward and, if followed correctly, can eliminate most hydraulic component failures. Preventive Maintenance is a discipline and must be followed as such in order to obtain results. We must view a PM program as performance-oriented and not activity-oriented.
Many organizations have good PM procedures but do not require maintenance personnel to follow them or hold them accountable for the proper execution of these procedures. In order to develop a preventive maintenance program for your system, you must follow these steps:
1st: Identify the system operating condition.
- Does the system operate 24 hours a day, 7 days a week?
- Does the system operate at maximum flow and pressure 70% or better during operation?
- Is the system located in a dirty or hot environment?
2nd: What requirements does the Equipment Manufacturer state for preventive maintenance on the hydraulic system?
3rd: What requirements and operating parameters does the component manufacturer state concerning the hydraulic fluid ISO particulate?
4th: What requirements and operating parameters does the filter company state concerning their filter’s ability to meet this requirement?
5th: What equipment history is available to verify the above procedures for the hydraulic system?
As in all preventive maintenance programs, we must write the procedures required for each PM Task. Steps or procedures must be written for each task and accurate and understandable by all maintenance personnel from entry-level to master.
Preventive maintenance procedures must be a part of the PM Job Plan which includes:
- Tools or special equipment required to perform the task.
- Parts or materials needed to perform the procedure with the store room number.
- Safety precautions for this procedure.
- Environmental concerns or potential hazards.
A list of preventive maintenance tasks for a hydraulic system could be:
- Change the hydraulic filter (the return or pressure filter).
- Obtain a hydraulic fluid sample.
- Filter hydraulic fluid.
- Check hydraulic actuators.
- Clean the inside of a hydraulic reservoir.
- Clean the outside of a hydraulic reservoir.
- Check and record hydraulic pressures.
- Check and record pump flow.
- Check hydraulic hoses, tubing, and fittings.
- Check and record voltage reading to proportional or servo valves.
- Check and record the vacuum on the suction side of the pump.
- Check and record amperage on the main pump motor.
- Check machine cycle time and record.
Preventive maintenance is the core support that a hydraulic system must have in order to maximize component and life and reduce system failure. Preventive maintenance procedures that are properly written and followed will allow equipment to operate to its full potential and life cycle.
Preventive maintenance allows a maintenance department to control a hydraulic system rather than the system controlling the maintenance department. We must maintain a hydraulic system by telling it when we will perform maintenance on it and how much money we will spend on its maintenance. Most companies allow the hydraulic system to control their maintenance at a much higher cost.
In order to validate your preventive maintenance procedures, you must have a good understanding of and knowledge of the “best maintenance practices” for hydraulic systems. We will convey these practices to you.
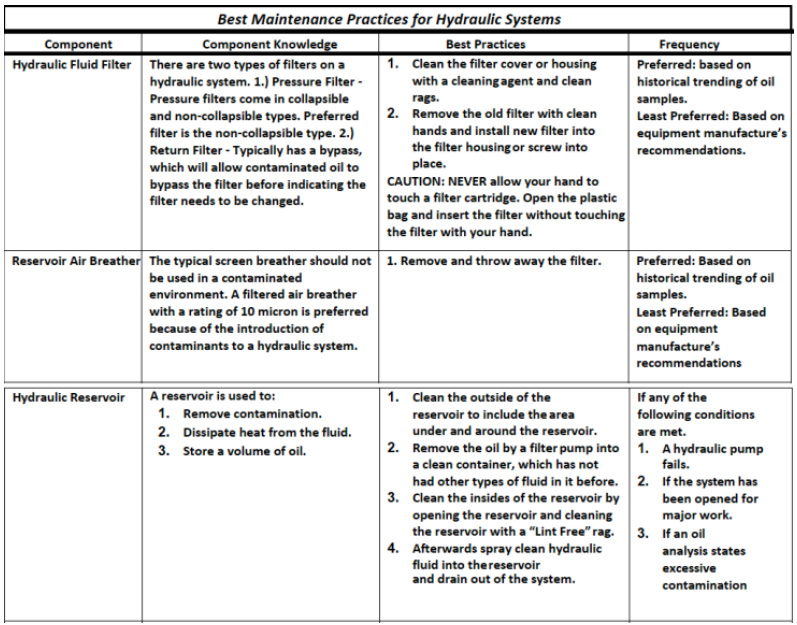
Maintenance Best Practices for Hydraulic Systems
Hydraulic Knowledge
People say knowledge is power. Well, this is also true in hydraulic maintenance. Many maintenance organizations do not know what their maintenance personnel should know.
I believe an industrial maintenance organization should divide the hydraulic skills necessary into two groups. One is the hydraulic troubleshooter; they must be your experts in maintenance, and this should be, as a rule of thumb, 10% or less of your maintenance workforce.
The other 90% + would be your general hydraulic maintenance personnel. They are the personnel that provide the preventive maintenance expertise. The percentages I gave you are based on a company developing a true Preventive / Proactive maintenance approach to their hydraulic systems. Let’s talk about hydraulic troubleshooter knowledge and skills.
Hydraulic Troubleshooting
Knowledge
- Mechanical Principles/force, work, rate, simple machines
- Math / basic math, complex math equations
- Hydraulic Components/application and function of all hydraulic system components.
- Hydraulic Schematic Symbols / understanding all symbols and their relationship to a hydraulic system.
- Calculate flow, pressure, and speed.
- Calculate the system filtration necessary to achieve the system’s proper ISO particulate code.
Skill
- Trace a hydraulic circuit to 100% proficiency.
- Set the pressure on a pressure-compensated pump.
- Tune the voltage on an amplifier card.
- Null a servo valve.
- Troubleshoot a hydraulic system and utilize “Root Cause Failure Analysis.”
- Replace any system component according to the manufacturer’s specifications.
- Develop a PM Program for a hydraulic system.
- Flush a hydraulic system after a major component failure.
General Hydraulic
Knowledge
- Filters/function, application, installation techniques
- Reservoirs/function, application
- Basic hydraulic system operation
- Cleaning of hydraulic systems
- Hydraulic lubrication principles
- Proper PM techniques for hydraulics
Skill
- Change a hydraulic filter and other system components.
- Clean a hydraulic reservoir.
- Perform PM on a hydraulic system.
- Change a strainer on a hydraulic pump.
- Add filtered fluid to a hydraulic system.
- Identify potential problems in a hydraulic system.
- Change a hydraulic hose, fitting, or tubing.
Measuring Success
Track hydraulic system fluid analysis. Track the following from the results. Take samples once a month for …
- Copper content
- Silicon content
- H2O
- Iron content
- ISO particulate count
- Fluid condition (viscosity, additives, and oxidation).
When the tracking process begins, you need to trend the information that can be trended. This allows management the ability to identify trends that can lead to positive or negative consequences.
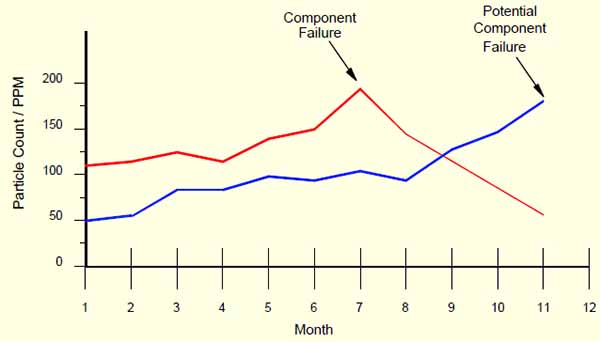
Press Hydraulic System. Hydraulic Fluid Sample Example.
Fluid analysis proved the need for better filtration. The addition of a 3-micron absolute return line filter to supplement the “kidney loop” filter solved the problem.
Many organizations do not know where to find the method for tracking and trending the information you need accurately. A sound Computerized Maintenance Management System can track and trend most of this information for you and allow Maintenance Technicians in the field to identify parts, material, etc., effectively and efficiently using cell phones.
Recommended Maintenance Modifications to an Existing Hydraulic System
Modifications to an existing hydraulic system need to be accomplished professionally. Modifications to hydraulic systems to improve maintenance efficiency are important to a company’s goal of maximum equipment reliability and reduced maintenance cost.
1. Filtration Pump with Accessories (Critical)
Objective: This pump modification aims to reduce contamination introduced into an existing hydraulic system by adding new fluid and the device used to add oil to the system.
Additional Information: Hydraulic fluid from the distributor is usually not filtered to the requirements of an operating hydraulic system. Typically, this oil is strained to a mesh rating, not a micron rating.
How clean is clean? Usually, hydraulic fluid must be filtered to 10 microns absolute or less for most hydraulic systems; 25 microns is the size of a white blood cell, and 40 microns is the lower limit of visibility with the unaided eye.
Many maintenance organizations still add hydraulic fluid to a system through a contaminated funnel. They may even use a bucket that previously had other types of fluids and lubricants without cleaning them.
Recommended Equipment and Parts
- Portable filter pump with a filter rating of 3 microns absolute.
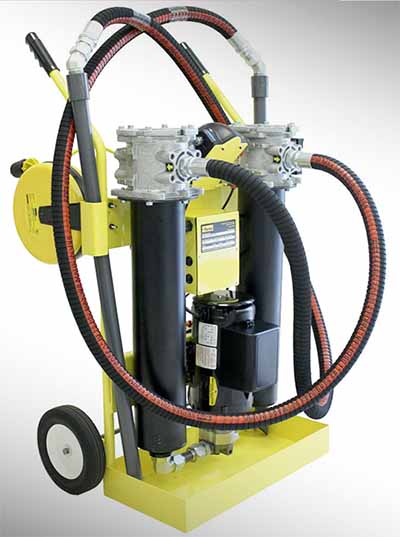
Filter Pump Unit Example
- Quick disconnects that meet or exceed the flow rating of the Portable Filter Pump.
- A ¾” pipe long enough to reach the bottom of a hydraulic container your fluids are delivered in from the distributor.
- If you receive your fluid by the drum, a 2″ reducer bushing to ¾” npt to fit into the 55-gallon drum. Otherwise, mount the filter buggy to the double wall “tote” tank supports if you receive larger quantities.
2. Modify the Hydraulic Reservoir
Objective: The objective is to eliminate the introduction of contamination through oil being added to the system or contaminates being added through the air intake of the reservoir. A valve needs to be installed for oil sampling.
Additional Information: If the hydraulic reservoir cycles, the air breather strainer should be replaced with a 10-micron filter. A quick disconnect should be installed on the bottom of the hydraulic unit and at the ¾ level point on the reservoir with valves to isolate the quick disconnects in case of failure.
As previously discussed, this allows the oil to be added from a filter pump and allows for external filtering of the hydraulic reservoir oil if needed. Install a petcock valve on the front of the reservoir that will be used for consistent oil sampling.
Equipment and Parts Needed
- Quick disconnects that meet or exceed the flow rating of the Portable Filter Pump.
- Two gate valves with pipe nipples.
- One 10-micron filter breather.
WARNING: Do not weld on a hydraulic reservoir to install the quick disconnects or air filter.
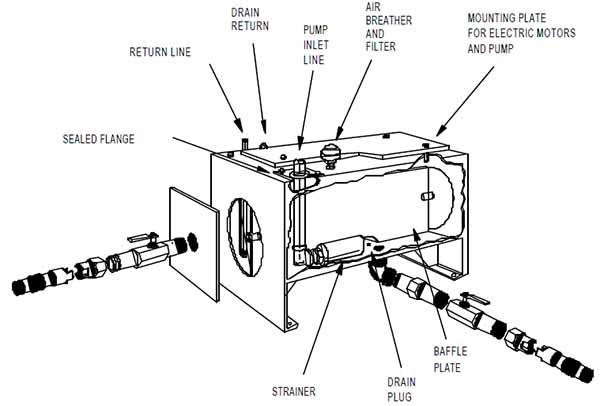
Hydraulic Reservoir Modification
Hydraulic System Root Cause Failure Analysis
As in any proactive maintenance organization, you must perform Root Cause Failure Analysis in order to eliminate future component failures. Most maintenance problems or failures will repeat themselves without someone identifying what caused the failure and proactively removing it. A preferred method is to inspect and analyze all component failures. Identify the following:
- Component Name and model number.
- Location of the component at the time of failure.
- Sequence or activity the system was operating at when the failure occurred.
- What caused the failure?
- How will the failure be prevented from happening again?
Failures are not caused by an unknown factor like “bad luck,” “it just happened,” or “the manufacturer made a bad part.” We have found most failures can be analyzed and prevention taken to prevent their reoccurrence. Establishing teams to review each failure can pay off in major ways.
To summarize, maintenance of a hydraulic system is the first line of defense to prevent component failure and thus improve equipment reliability. As spoken about earlier, discipline is the key to the success of any proactive maintenance program.